Hallo zusammen!
ich bin gerade dabei meine Eigenbaufräse zu konstruieren. Im Paralleluniversum gibt es bereits ein Thread, da dort aber leider kaum noch konstuktive Rückmeldungen kommen und hier, bezüglich Eigenbau, qualitativ und quantitativ mehr los ist, möchte ich die Diskussion gern hier weiterführen. Bisher wurden ein paar Konzepte zur Ausführung des Portals mit Y- und Z-Achse diskutiert. Hier hat Karl schon tatkräftig mitgewirkt.
Hier ein Paar Eckdaten:
Ich bin sehr günstig an ABBA Linearführungen gekommen und werde diese für meine Fräse einsetzen. Die Verfahrwege sind folgendermaßen geplant:
X= ca. 1040 mm
Y= ca. 560 mm
Z = max. 200 mm eher weniger
Als Steuerung soll das bekannte TripleBeast eingesetzt werden. Mit der Fräse soll: Depron, Schaum, Formenmaterial, Holz, Kuststoff über GFK und CFK bis hin zu Aluminium gefräst werden.
Die Konstruktion der X-,Y-Achse steht weitestgehend fest. Hier werde ich zu Gunsten der Steifigkeit, den Verfahrweg der Z-Achse (bisher waren 200 mm angedacht) nochmal überdenken bzw. reduzieren.
Für die statische Auslegung der Komponenten rechne ich mit 100N an der Fräserspitze. Die momentanen Werte der Durchbiegungen des jetzigen Konstruktionsstandes werde ich mal aufbereiten und hier einstellen.
Zu den Möglichkeiten: Ich arbeite seit 2,5 Jahren als Konstrukteur im Maschinebau/Automatisierungstechnik. Dadruch habe ich die Möglichkeit, die Bauteile in der Firma fertigen zu lassen. Im CAD Bereich nutzen wir Inventor, welches ich für die 3D Konstruktion der Fräse nutze.
Hier der bisherige Entwurfsstand
Fräse:
Auf der X-Achse sollten 25 ger und auf der Y- und Z-Achse 20 ger Kugelumlaufführungen eingesetzt werden.
Y-Z-Ache:
Was ist geplant?
Ich bin momentan am überlegen ob ich bei dem Grundgestell doch auf eine Schweisskonstruktion gehe. Ich werde das konstruktiv mal betrachten und rechnen. Außerdem werde ich den Zusatzaufwand abschätzen und Vor- und Nachteile bewerten. Die Ausführung mit Schweissgestell würde ich generell so umsetzen wie auch das Gestell aus Al-Profilen (Führungen seitlich, usw).
Dann ziehe ich als Alternative für das schwere 160x80 ger Al-Profil des Portalbalkens eine Schweisskonstruktion aus Alu Rechteckrohr mit aufgeschweissten Flacheisen in betracht. Das würde deutlich Gewicht sparen und wäre bezüglich Biegesteifigkeit sehr ähnlich und die Torsionssteifigkeit ist besser.
Hier habe ich zwei Konzepte. Das Erste besteht aus einem Rechteckrohr 160x80x4. Im Bereich der Führungen wird Aluflach aufgeschweisst. Seitlich wird das Profil mit Aluflach verschlossen. Die Anschraubflächen der Führungen und die seitlichen Kontaktflächen werden bearbeitet und in die seitlichen Flächen werden Gewinde geschnitten.
Das Zweite Konzept ist ähnlich aufgebaut. Es besteht aus zwei Quardatrohren 80x80x4.
Der Grund für das zweite Konzept sind Bedenken, ob die Bereiche der angeschraubten Führungen steif genug sind. Wenn das Rohr in diesem Bereich bei Belastung der Führungen "atmet", dann hat das Ungenauigkeiten zur Folge. Alles im tausendstel bis hundertstel Bereich versteht sich. Die beiden Profile und die Flacheisen werden mit unterbrochenen bzw. durchgehenden Schweissnähten verschweisst werden.
Die Hauptvorteile der beiden Varianten wäre das geringere Gewicht. Hier mal die relevanten Werte im Vergleich.
ITEM 160x80 natur
Flächenträgheitsmoment um X = 12.283.300 mm^4
Flächenträgheitsmoment um Z = 3.608.900 mm^4
Torsionsflächenmoment = 3.974.100 mm^4
Durchbiegung bei zwei Auflagern und 100 N mittig um X = 0,0009 mm
Durchbiegung bei zwei Auflagern und 100 N mittig um Y = 0,003 mm
Gewicht bei 730 mm Länge = 9,86 kg
Rechteckrohr 160x80
Flächenträgheitsmoment um X = 7.320.114 mm^4
Flächenträgheitsmoment um Z = 2.643.321 mm^4
Torsionsflächenmoment = 4.847.059 mm^4
Durchbiegung bei zwei Auflagern und 100 N mittig um X = 0,0016 mm
Durchbiegung bei zwei Auflagern und 100 N mittig um Y = 0,004 mm
Gewicht bei 730 mm Länge = 5,2 kg
2x Quadratrohr 160x80
Flächenträgheitsmoment um X = 7.324.102 mm^4
Flächenträgheitsmoment um Z = 2.914.839 mm^4
Torsionsflächenmoment = muss mal gucken wie ich das rechne (Abschätzung: besser als Variante 2)
Durchbiegung bei zwei Auflagern und 100 N mittig um X = 0,0016 mm
Durchbiegung bei zwei Auflagern und 100 N mittig um Y = 0,004 mm
Gewicht bei 730 mm Länge = 6,3 kg
Sicher ist der Fertigungsaufwand höher, aber die Gewichtseinsparnis ist meiner Meinung nach nicht zu verachten.
Wie schon geschrieben, werde ich die errechneten Durchbiegungen mal zusammen schreiben, damit die Gesamtauslegung durchsichtiger wird. Gerade der Portalbaklen ist hier deutlich überdimensioniert. Der Grund dafür ist aber die nötige Bauhöhe, um beide Y-Führungen vorn vor dem Balken positionieren zu können.
Gruß Marc
ich bin gerade dabei meine Eigenbaufräse zu konstruieren. Im Paralleluniversum gibt es bereits ein Thread, da dort aber leider kaum noch konstuktive Rückmeldungen kommen und hier, bezüglich Eigenbau, qualitativ und quantitativ mehr los ist, möchte ich die Diskussion gern hier weiterführen. Bisher wurden ein paar Konzepte zur Ausführung des Portals mit Y- und Z-Achse diskutiert. Hier hat Karl schon tatkräftig mitgewirkt.
Hier ein Paar Eckdaten:
Ich bin sehr günstig an ABBA Linearführungen gekommen und werde diese für meine Fräse einsetzen. Die Verfahrwege sind folgendermaßen geplant:
X= ca. 1040 mm
Y= ca. 560 mm
Z = max. 200 mm eher weniger
Als Steuerung soll das bekannte TripleBeast eingesetzt werden. Mit der Fräse soll: Depron, Schaum, Formenmaterial, Holz, Kuststoff über GFK und CFK bis hin zu Aluminium gefräst werden.
Die Konstruktion der X-,Y-Achse steht weitestgehend fest. Hier werde ich zu Gunsten der Steifigkeit, den Verfahrweg der Z-Achse (bisher waren 200 mm angedacht) nochmal überdenken bzw. reduzieren.
Für die statische Auslegung der Komponenten rechne ich mit 100N an der Fräserspitze. Die momentanen Werte der Durchbiegungen des jetzigen Konstruktionsstandes werde ich mal aufbereiten und hier einstellen.
Zu den Möglichkeiten: Ich arbeite seit 2,5 Jahren als Konstrukteur im Maschinebau/Automatisierungstechnik. Dadruch habe ich die Möglichkeit, die Bauteile in der Firma fertigen zu lassen. Im CAD Bereich nutzen wir Inventor, welches ich für die 3D Konstruktion der Fräse nutze.
Hier der bisherige Entwurfsstand
Fräse:
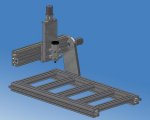
Auf der X-Achse sollten 25 ger und auf der Y- und Z-Achse 20 ger Kugelumlaufführungen eingesetzt werden.
Y-Z-Ache:
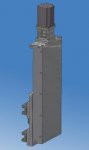
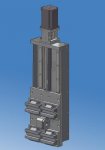

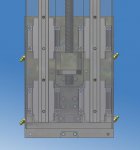
Was ist geplant?
Ich bin momentan am überlegen ob ich bei dem Grundgestell doch auf eine Schweisskonstruktion gehe. Ich werde das konstruktiv mal betrachten und rechnen. Außerdem werde ich den Zusatzaufwand abschätzen und Vor- und Nachteile bewerten. Die Ausführung mit Schweissgestell würde ich generell so umsetzen wie auch das Gestell aus Al-Profilen (Führungen seitlich, usw).
Dann ziehe ich als Alternative für das schwere 160x80 ger Al-Profil des Portalbalkens eine Schweisskonstruktion aus Alu Rechteckrohr mit aufgeschweissten Flacheisen in betracht. Das würde deutlich Gewicht sparen und wäre bezüglich Biegesteifigkeit sehr ähnlich und die Torsionssteifigkeit ist besser.
Hier habe ich zwei Konzepte. Das Erste besteht aus einem Rechteckrohr 160x80x4. Im Bereich der Führungen wird Aluflach aufgeschweisst. Seitlich wird das Profil mit Aluflach verschlossen. Die Anschraubflächen der Führungen und die seitlichen Kontaktflächen werden bearbeitet und in die seitlichen Flächen werden Gewinde geschnitten.
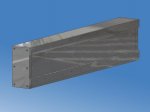
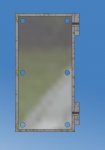
Das Zweite Konzept ist ähnlich aufgebaut. Es besteht aus zwei Quardatrohren 80x80x4.
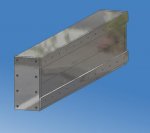
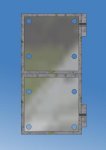
Der Grund für das zweite Konzept sind Bedenken, ob die Bereiche der angeschraubten Führungen steif genug sind. Wenn das Rohr in diesem Bereich bei Belastung der Führungen "atmet", dann hat das Ungenauigkeiten zur Folge. Alles im tausendstel bis hundertstel Bereich versteht sich. Die beiden Profile und die Flacheisen werden mit unterbrochenen bzw. durchgehenden Schweissnähten verschweisst werden.
Die Hauptvorteile der beiden Varianten wäre das geringere Gewicht. Hier mal die relevanten Werte im Vergleich.
ITEM 160x80 natur
Flächenträgheitsmoment um X = 12.283.300 mm^4
Flächenträgheitsmoment um Z = 3.608.900 mm^4
Torsionsflächenmoment = 3.974.100 mm^4
Durchbiegung bei zwei Auflagern und 100 N mittig um X = 0,0009 mm
Durchbiegung bei zwei Auflagern und 100 N mittig um Y = 0,003 mm
Gewicht bei 730 mm Länge = 9,86 kg
Rechteckrohr 160x80
Flächenträgheitsmoment um X = 7.320.114 mm^4
Flächenträgheitsmoment um Z = 2.643.321 mm^4
Torsionsflächenmoment = 4.847.059 mm^4
Durchbiegung bei zwei Auflagern und 100 N mittig um X = 0,0016 mm
Durchbiegung bei zwei Auflagern und 100 N mittig um Y = 0,004 mm
Gewicht bei 730 mm Länge = 5,2 kg
2x Quadratrohr 160x80
Flächenträgheitsmoment um X = 7.324.102 mm^4
Flächenträgheitsmoment um Z = 2.914.839 mm^4
Torsionsflächenmoment = muss mal gucken wie ich das rechne (Abschätzung: besser als Variante 2)
Durchbiegung bei zwei Auflagern und 100 N mittig um X = 0,0016 mm
Durchbiegung bei zwei Auflagern und 100 N mittig um Y = 0,004 mm
Gewicht bei 730 mm Länge = 6,3 kg
Sicher ist der Fertigungsaufwand höher, aber die Gewichtseinsparnis ist meiner Meinung nach nicht zu verachten.
Wie schon geschrieben, werde ich die errechneten Durchbiegungen mal zusammen schreiben, damit die Gesamtauslegung durchsichtiger wird. Gerade der Portalbaklen ist hier deutlich überdimensioniert. Der Grund dafür ist aber die nötige Bauhöhe, um beide Y-Führungen vorn vor dem Balken positionieren zu können.
Gruß Marc
Zuletzt bearbeitet: