Ich wollte schon immer einen Hexa haben und inspiriert von Ferdl's Langzeit-Pionierarbeit war ich auch mal wieder reif. Ein neuer Copter musste her, diesmal was Grosses. Nach Quadrixette 30, Schrott-o-Copter 20cm und Speedy 350 eben 1,5m Spannweite.
Der Plan ist einfach: Gross, Hexa, cooles Design, lange Flugzeit.
Ein paar Anläufe hat es gebraucht, bis das halbwegs getaugt hat:
A) Ab hier hat mir das Design ganz gut gefallen
B) Hier war die Idee mit überkreuzten Rohen mehr Stabilität in den Riesenrahmen zu bringen
C) Und das war schon fast der finale Entwurf
Geworden ist es dann doch das hier:
Die überkreuzten Rohre hatte ich dann doch wieder verworfen. Zum einen wegen Kabelzuführung, gekreuzte hätten anbohren gebraucht. Zum anderen wegen den notwendigen Spezialschellen auf den Kreuzungen, die hätten einen 3D-Drucker gebraucht. Ich wollte da aber schon unbedingt die Centerplates sehen und Shapeways braucht ja ne gefühlte Ewigkeit.
Dass der Schwerpunkt halbwegs in der Mitte liegt ist rein per Hüftgefühl und Daumenwert ermittelt: Welches Gewicht wird wo hängen (vorne soll später mal ein Gimbal hin), wie wird es auf der gegenüberliegenden Seite austariert. Deswegen schwere Akkus am kurzen Heck und vergleichsweise leichtes Gimbal an der Front auf doppelter Entfernung. Ebenso sollten die Props halbwegs ausgeglichen Schub auf Vorne/Hinten bringen. Ob das wirklich so hinkommt, wird sich noch rausstellen. Klar war auch, dass es vermutlich eine Herausforderung wird, dass das CP-Sandwich halbwegs steif wird.
So kam es dann aus der Fräse (nachdem mein zeichnerisches Debakel bereinigt wurde
:
Grösse 1050 x 520 x 2,5mm GFK. An dieser Stelle nochmal tausend Dank an Joachim (mal wieder) für den Hammerjob (und die permanente Hilfe, Nacharbeit, etc. Ähem
)! Daran wird jetzt getestet, wenn alles funktioniert, später überarbeitet und final in CFK.
Erkenntnis: Ist ordentlich steif. Bei CFK könnte ich vermutlich mit 1,8mm Dicke hinkommen, wenn noch etwas zusätzlich versteift wird. Und: GFK in 2,5mm ist auch ordentlich schwer.
Wenig später lag es so auf der Werkbank:
Das sind die FCP HL Schellen aus POM von Paul. Die breiten Schellen haben mir gut gefallen (auch als zusätzliche Rahmenversteifung, die haben nämlich noch einen Mittelpin). Und für die Auslegerenden gibts Kabelschützern mit LED (a bisserl Christbaum muss auch sein).
Die Rohre mal testweise angelegt (dank an Jever):
Die 12mm Rohre (streng nach Ferdl-Empfehlung) hatte ich da, auf 1m Länge haben sie sich aber doch ganz gut durchgebogen, so dass ich nochmal gegen 16mm (streng nach Ferdl-Empfehlung) getauscht hab. Die 16mm von Carbon Comp. sind ordentlich steif (und edel), die 22mm kann man sich imho sparen.
Hier sieht man deutlich den Hangar für die kleineren Copter, den Aufzug zum Flugdeck baue ich später ein.
Ausblick auf den späteren Look, musste sein:
Materialschlacht zum Ersten (dank an Erdinger (alloholfrei)):
6 Coax-Ausleger wollen gebastelt werden, die ESCs kommen ans Auslegerende zwecks Gewichtseinsparung (Kabel). Die Schellen werden angebohrt, um darin die Halteplatten für die ESCs per Kabelbinder festmachen zu können.
Das war Arbeit:
Die Zylinderkopfschrauben wurden durch Sechskant ersetzt, um überhaupt mit den Schlüsseln noch auf den Schraubkopf zu kommen. Gottseidank sind die selbstsichernden Muttern vom Paul nicht magnetisch, hatte mal kurz nicht selbstsichernde magnetische probiert. 20 Minuten Fluchen, mehr sag ich nicht dazu.
Materialschlacht zum Zweiten: 14x SimonK will hier drauf.
Dirty Deeds done dirt cheap:
Irgendwann ist es dann soweit:
Geflasht (normal/reverse), Wärmeleitpaste anstatt Plaste, entbranded, Luftloch, getestet. BlueSeries 12A für 4S (mutig ja, aber auch schon praxisgetestet), wiegen nur die Hälfte der 20A's.
Wieder 120 Lötpunkte später:
250g pro Ausleger macht dann 1,5kg insgesamt. Prognose: 3kg für den kompletten Frame ohne Akkus.
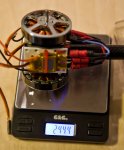
Der Plan ist einfach: Gross, Hexa, cooles Design, lange Flugzeit.
Ein paar Anläufe hat es gebraucht, bis das halbwegs getaugt hat:
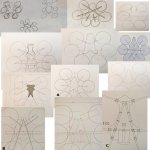
A) Ab hier hat mir das Design ganz gut gefallen
B) Hier war die Idee mit überkreuzten Rohen mehr Stabilität in den Riesenrahmen zu bringen
C) Und das war schon fast der finale Entwurf
Geworden ist es dann doch das hier:
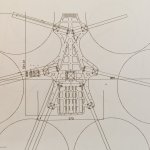
Die überkreuzten Rohre hatte ich dann doch wieder verworfen. Zum einen wegen Kabelzuführung, gekreuzte hätten anbohren gebraucht. Zum anderen wegen den notwendigen Spezialschellen auf den Kreuzungen, die hätten einen 3D-Drucker gebraucht. Ich wollte da aber schon unbedingt die Centerplates sehen und Shapeways braucht ja ne gefühlte Ewigkeit.
Dass der Schwerpunkt halbwegs in der Mitte liegt ist rein per Hüftgefühl und Daumenwert ermittelt: Welches Gewicht wird wo hängen (vorne soll später mal ein Gimbal hin), wie wird es auf der gegenüberliegenden Seite austariert. Deswegen schwere Akkus am kurzen Heck und vergleichsweise leichtes Gimbal an der Front auf doppelter Entfernung. Ebenso sollten die Props halbwegs ausgeglichen Schub auf Vorne/Hinten bringen. Ob das wirklich so hinkommt, wird sich noch rausstellen. Klar war auch, dass es vermutlich eine Herausforderung wird, dass das CP-Sandwich halbwegs steif wird.
So kam es dann aus der Fräse (nachdem mein zeichnerisches Debakel bereinigt wurde
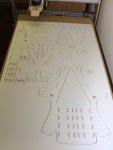
Grösse 1050 x 520 x 2,5mm GFK. An dieser Stelle nochmal tausend Dank an Joachim (mal wieder) für den Hammerjob (und die permanente Hilfe, Nacharbeit, etc. Ähem
Erkenntnis: Ist ordentlich steif. Bei CFK könnte ich vermutlich mit 1,8mm Dicke hinkommen, wenn noch etwas zusätzlich versteift wird. Und: GFK in 2,5mm ist auch ordentlich schwer.
Wenig später lag es so auf der Werkbank:
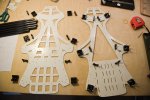
Das sind die FCP HL Schellen aus POM von Paul. Die breiten Schellen haben mir gut gefallen (auch als zusätzliche Rahmenversteifung, die haben nämlich noch einen Mittelpin). Und für die Auslegerenden gibts Kabelschützern mit LED (a bisserl Christbaum muss auch sein).
Die Rohre mal testweise angelegt (dank an Jever):
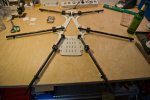
Die 12mm Rohre (streng nach Ferdl-Empfehlung) hatte ich da, auf 1m Länge haben sie sich aber doch ganz gut durchgebogen, so dass ich nochmal gegen 16mm (streng nach Ferdl-Empfehlung) getauscht hab. Die 16mm von Carbon Comp. sind ordentlich steif (und edel), die 22mm kann man sich imho sparen.
Hier sieht man deutlich den Hangar für die kleineren Copter, den Aufzug zum Flugdeck baue ich später ein.
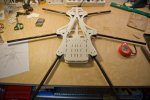
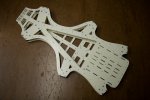
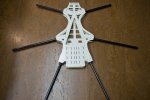
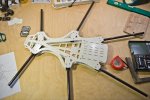
Ausblick auf den späteren Look, musste sein:
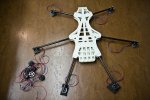
Materialschlacht zum Ersten (dank an Erdinger (alloholfrei)):
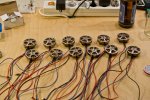
6 Coax-Ausleger wollen gebastelt werden, die ESCs kommen ans Auslegerende zwecks Gewichtseinsparung (Kabel). Die Schellen werden angebohrt, um darin die Halteplatten für die ESCs per Kabelbinder festmachen zu können.
Das war Arbeit:
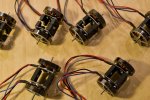
Die Zylinderkopfschrauben wurden durch Sechskant ersetzt, um überhaupt mit den Schlüsseln noch auf den Schraubkopf zu kommen. Gottseidank sind die selbstsichernden Muttern vom Paul nicht magnetisch, hatte mal kurz nicht selbstsichernde magnetische probiert. 20 Minuten Fluchen, mehr sag ich nicht dazu.
Materialschlacht zum Zweiten: 14x SimonK will hier drauf.
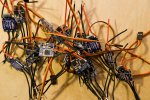
Dirty Deeds done dirt cheap:
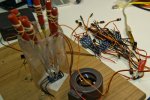
Irgendwann ist es dann soweit:
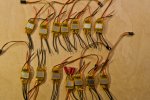
Geflasht (normal/reverse), Wärmeleitpaste anstatt Plaste, entbranded, Luftloch, getestet. BlueSeries 12A für 4S (mutig ja, aber auch schon praxisgetestet), wiegen nur die Hälfte der 20A's.
Wieder 120 Lötpunkte später:
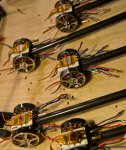
250g pro Ausleger macht dann 1,5kg insgesamt. Prognose: 3kg für den kompletten Frame ohne Akkus.
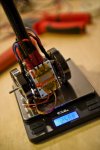
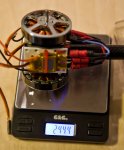
Zuletzt bearbeitet: